Cutting tool is a wedge shaped device that actually removes (shears off) excess material from a preformed blank (workpiece) in order to obtain desired shape, size and accuracy. So cutting tool is indispensably necessary device for machining or metal cutting operation. Geometry, orientation and material are the three important factors to consider for a cutting tool. Although basic shape of cutting tool varies greatly with the type of operation it is intended to perform, every cutting tool must contain a wedge shaped portion with a sharp cutting edge. Material from the workpiece is actually cut by this cutting edge.
Classification of cutting tools – Single point, Double point and Multi-point
A cutting tool may contain one or more main cutting edges that participate in cutting action at a time in a single pass. Cutting tools can be classified in various ways; however, the most common way is based on the number of main cutting edges that participates in cutting action at a time. On this basis, cutting tools can be classified into three groups, as given below.
- Single point cutting tool
- Double point cutting tool
- Multi point cutting tool
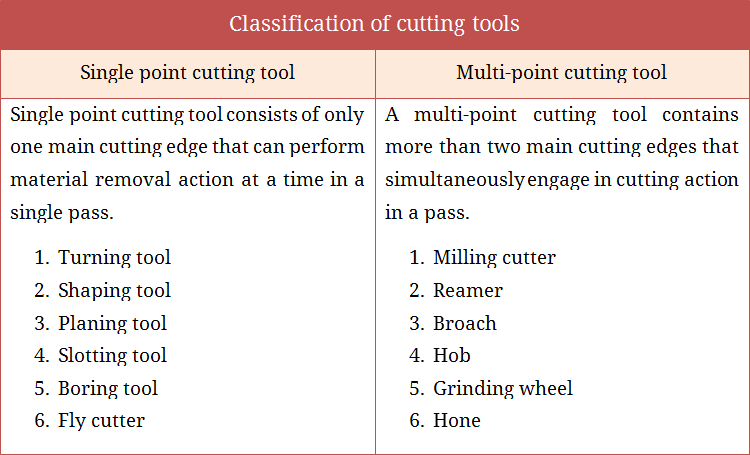
Single point cutting tools
As the name suggests, single point cutting tools consist of only one working cutting edge that can perform metal removal action at a time. It is to be noted that, in insert based cutting tools, multiple cutting edges may present in a single tool; however, only one cutting edge can engage in material removal action at a time. Read details about single point cutting tool.
Example of single point cutting tool: Turning tool, also known as Single Point Turning Tool (SPTT), is the perfect example of a single point tool. Apart from turning tool, shaping, planing, slotting, boring tools are also single point tool.
Pros and cons: Design and fabrication of single point cutter is quite simple and less time consuming. However, tool wear rate is high and as a result tool life is low. Moreover, such tools cannot take high depth of cut or feed rate, and consequently, material removal rate (MRR) and productivity are lower.
Double point cutting tools
These tools contain two working cutting edges and both the edges can perform material removal action simultaneously. Sometime, cutters are classified into two groups—single point and multi-point cutters. In such scenario, double point cutters are also considered as multi point cutters. Read details about double point cutting tool.
Example of double point cutting tool: Drill is the only example for this category. Note that drills may have more than two cutting edges. However, conventional (without cutting edge modification) metal cutting drills contain two cutting edges.
Multi-point cutting tools
As the name suggests, multi-point cutting tools contain more than two working cutting edges. The number of cutting edges may vary from around four (in milling cutter) to hundreds (in grinding wheel). However, all cutting edges may not perform cutting action simultaneously; they can successively engage and disengage. Read details about multi point cutting tool.
Example of multi-point cutting tool: Milling cutters are the common example for this category. Apart from milling cutters, few other examples of multi-point cutter are Reamer (tool for reaming operation), Broach (tool for broaching operation), Hob (tool for hobbing operation), Grinding wheel (abrasive cutter), Hone (tool for honing operation), etc.
Pros and cons: Multi-point cutting tools provide high Material Removal Rate (MRR) as they can take substantially higher feed rate and depth of cut without failure. So use of such cutters is economically advantageous. Chip load on individual tooth is also considerably low as entire load is uniformly distributed into all teeth. However, machining with multi-point cutting tool is inherently intermittent cutting and thus fluctuation in cutting force, impact loading on teeth, vibration, etc. issues become predominant.
References
- Book: Machining and Machine Tools by A. B. Chattopadhyay.
- Book: Metal Cutting: Theory And Practice by A. Bhattacharya.
- Book: Manufacturing Process for Engineering Materials by S. Kalpakjain and S. Schmid.
- Book: Geometry of Single-point Turning Tools and Drills – Fundamentals and Practical Applications by V. P. Astakhov.